Working with Resin
Resin is a very versatile material for miniatures which has many advantages over metal or plastic. Here at Zealot, we believe resin is the best material for miniatures and so we cast most of our products in this material.
However, resin can be a bit different to work with if you are used to plastic or white metal models. This page will cover the stages you should go through when working with resin miniatures.
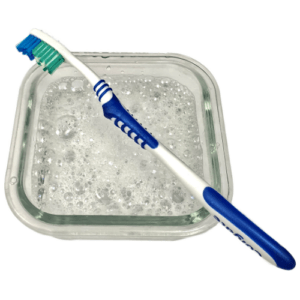
Optional Cleaning
You have just eagerly unpacked your awesome new miniatures, but before you go ahead gluing things together, you might like to clean them. This stage is optional, but it will get a better result and better paint and glue adhesion. Cleaning can be done because the moulds used to cast resin can leave the slightest oily residue on the model’s surface. Plus sometimes in order to keep casts the highest quality; we use some release agent, to get the miniatures out of their moulds more easily. The oil from the moulds or the release agent can repel paint and glue, so it is best that the surfaces are cleaned.
Use an old toothbrush and some warm water with ‘washing up liquid’ to gently brush the pieces clean (be extra careful of delicate pieces, so that you don’t snap them). Make sure you rinse the parts afterwards and allow them to thoroughly air-dry.
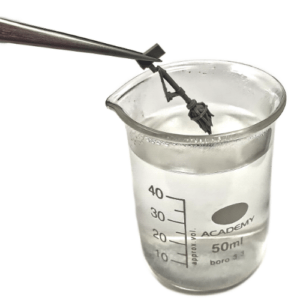
Bending
Resin is very detailed, yet sometimes thin parts may be bent slightly during transport or storage. It is simple to fix as resin has a “thermal memory” like a thermoplastic. It remembers the shape it was cast in. So simply run the part under a hot tap or use boiled water to heat and soften it. Then you can bend it carefully into shape. Let it cool by quenching in cool water, pretend you are a fantasy blacksmith and the resin will set like this in the shape you want.
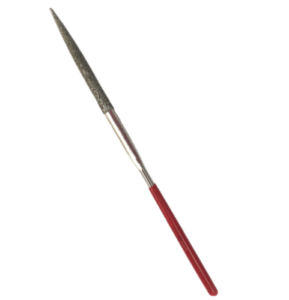
Tidying
At Zealot we try to produce minis without massive hideous mould lines, flash, vents, air bubbles or other things that cause you a headache. But, try as we might, we are not (yet!) perfect and sometimes you will need to call upon your hobby skills to tidy up a part. Just like you would with plastic minis – use some hobby clippers to snip off any casting gates (aka: those rods/sprues/ supports) Mould lines may need to be scraped or lightly sanded* away with a file or hobby knife and any flash can also be removed in this same way.
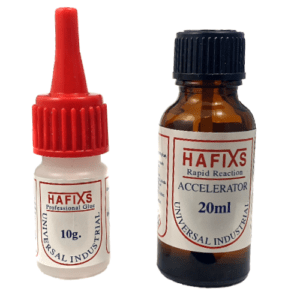
Gluing
To glue resin, you should use Super Glue Cyanoacrylate. If you rough up the surface of the bond with sandpaper or scratch it a bit first – you will get a stronger bond. Another good trick is to use water to make one part damp (not wet!) and apply the glue to the second part. The bond will be much quicker. You can also use superglue accelerator in the same way.
If you glue your fingers or something you want to remove the glue from, you can use pineapple juice (useful and delicious) or super glue remover.
Some larger pieces may need to be pinned in place like how you do with metal models. In rare cases for huge joins where you want the ultimate bond – Two part epoxy glue can be used.
All done, your model is cleaned, prepped and assembled
Now you are ready to prime your model as per usual and start painting. We recommend a light dusting with an aerosol spray primer or good airbrush primer.
Hopefully that helped cover a few of the main points with working with our resin. We wish you the best of luck with assembling and painting your miniatures.
Happy Hobbies!
*Resin is great, but be careful not to breathe in too much of the dust when sanding or drilling it. It can be harmful. So when making a lot of dust – either do this outside or use a face mask or dust mask.
For this reason, we don’t recommend resin miniatures to unsupervised persons under the age of 13.
Resin miniatures are not a toy. Small parts are a choking hazard to infants under the age of 3.