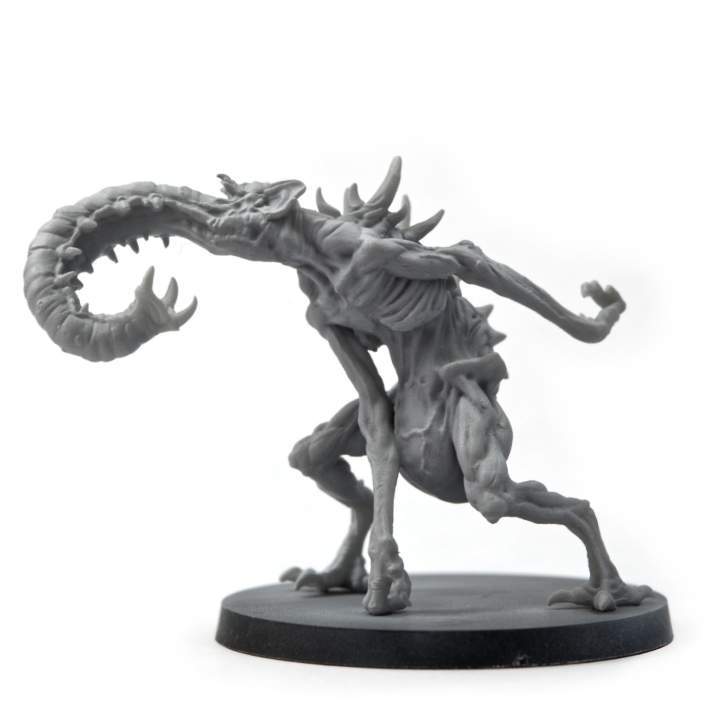
Why Manufacture with 3D Printing?
For short-run, complex products, direct 3D printing is a good solution. Hollow objects, parts with complex geometries, thin parts too fragile to demould or for small limited batches where a master prototype and mould making set up costs just don’t make sense.
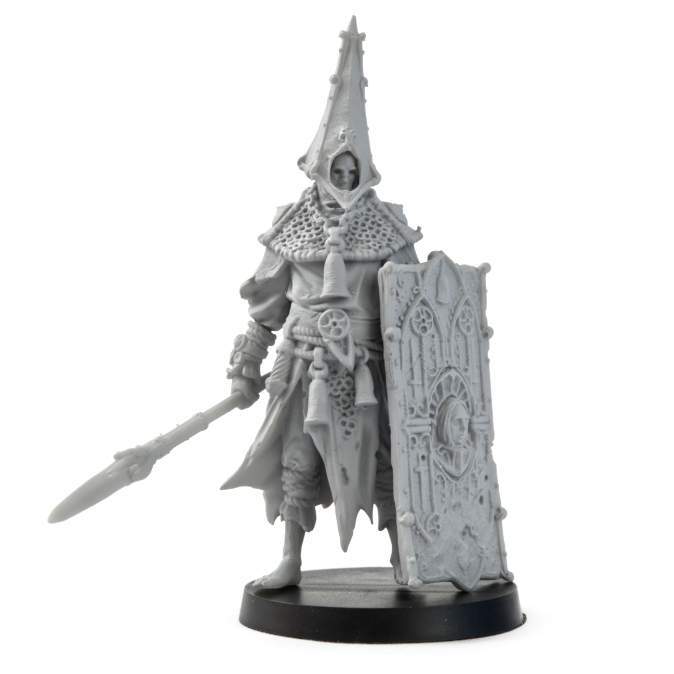
Detailed 3D Printed Manufacturing
If you are looking for direct 3D printed manufacturing for your products, we run a suite of Prozen Sonic 4k printers. These printers offer superb detail of 35 micron XY pixel size and 25 micron Z layers. Which ensures every detail of your sculpts are picked up. We have a 4 stage post-processing method to clean your prints as effectively as possible and make sure those details remain sharp and defined.
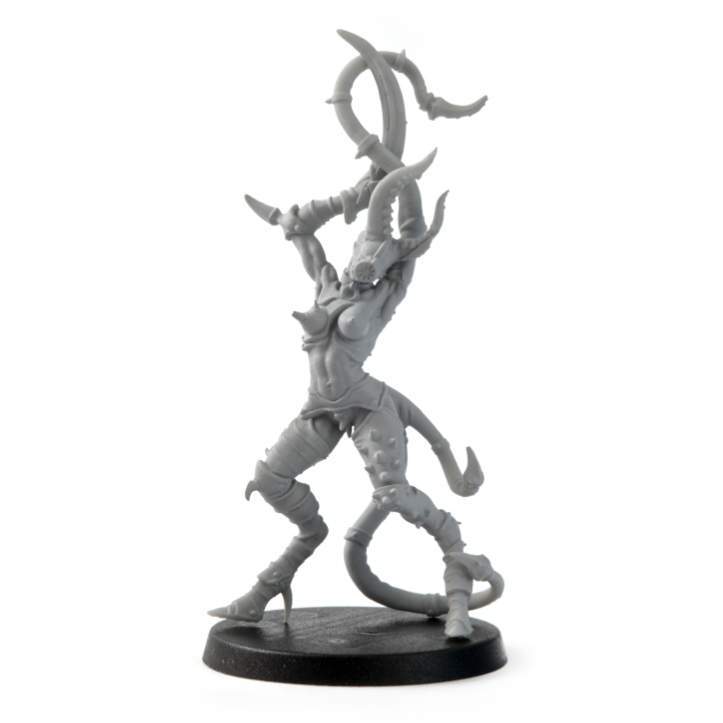
Just 10 Units Minimum Order
With just 10 units minimum order of each part, your investment in stock is very low. Our typical order turnaround time is 10 days for new products, and 7 days for repeat restock orders.
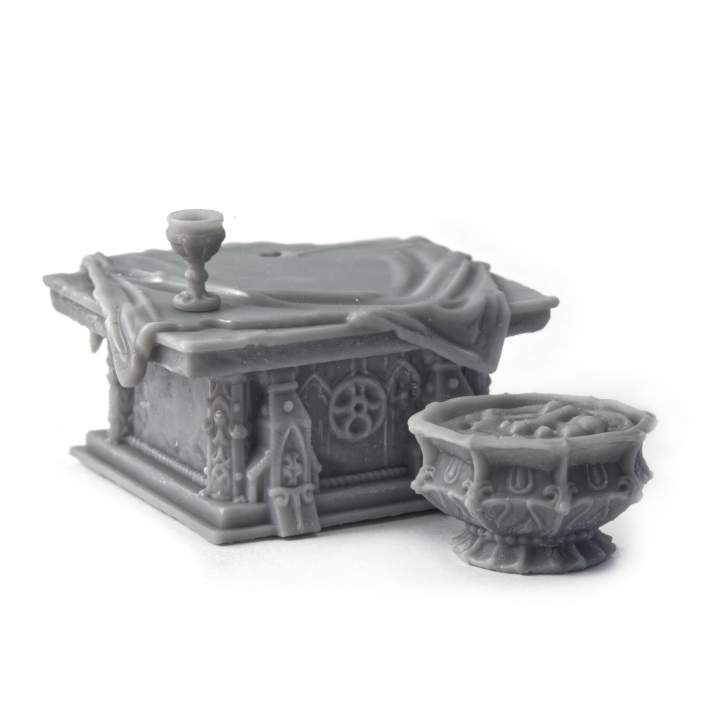
Limitations of 3D Printed Manufacture?
Of course there are some disadvantages of this process. So you can manage your expectations, you should bear in mind:
- It is slow, for large batches of prints. Each 3D print plate takes on average 13 hours.
- Support rods will need cleaning up. We supply prints with supports attached, your customers will have to remove these and sand the contacts.
- One-off set up cost, if your files are unsupported. It can take hours to set up good supports, this is charged if your files are provided to us unsupported.
- Detail is not as good as casting. Compared to using our Prototyping Services to produce an ultra-detailed master, and casting from this. 3D prints from these more economic machines are not as detailed.
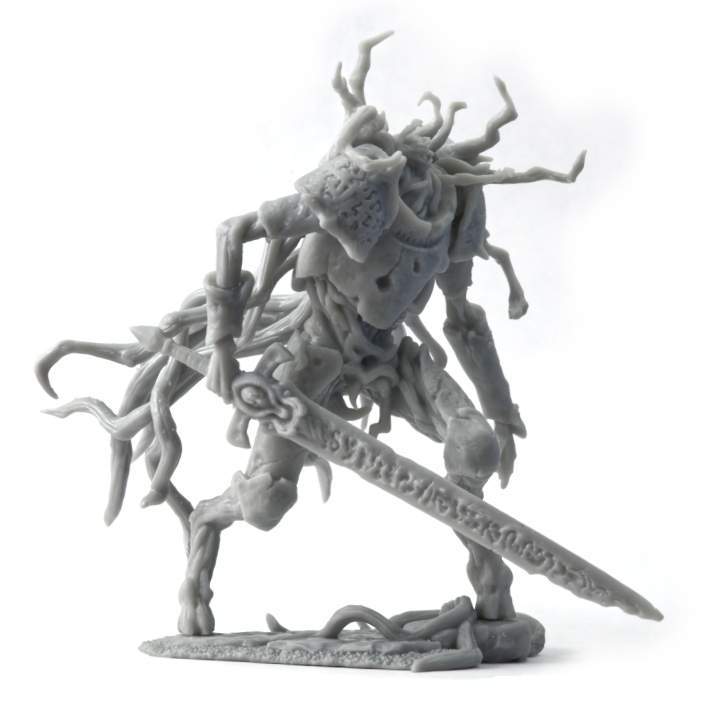
Benefits of 3D Printed Manufacture?
But this new type of 3D printed manufacturing does offer some strong advantages, when compared to traditional methods:
- No initial start-up cost. With no initial investment, providing us supported files – you just pay for what stock you need.
- No mould lines or complex assemblies. Where a part would have to be split into many pieces for casting, it can be 3D printed as one object. Meaning less seam lines and joins for customers to deal with. Plus, mould line free!
- Creative freedom. With none of the traditional limitations from undercuts, hollows, material shrinkages. Direct 3D printing has far less constraints than traditional manufacture.
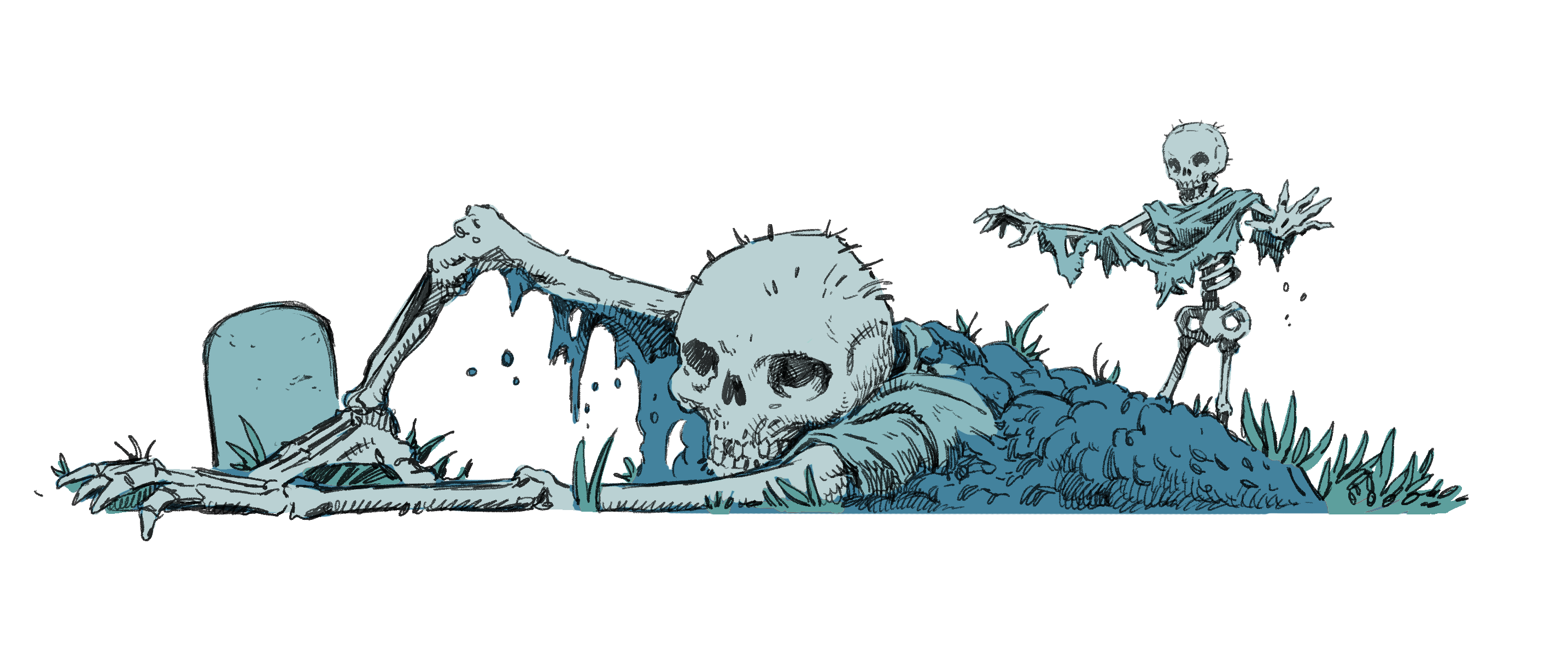